In the world of plastic manufacturing, choosing the right THY Precision injection molding machine types is key to top-notch quality control and better production. Ever thought about how new injection molding machine types could change your quality control game? Get ready to learn the secrets that can make your plastic parts stand out.
Key Takeaways
- Discover how advanced injection molding machine types can boost your quality control.
- Explore the wide variety of plastic injection molding machines and what they can do.
- Learn how the right injection molding machine types can meet your manufacturing needs.
- Find out about the latest in hydraulic injection molding machines, electric injection molding machines, and more.
- Get tips on how to make your production more efficient and reduce defects with the right injection molding machine types.
Introduction to Injection Molding Machines
Injection molding machine is key in making plastic injection molding work. It turns raw plastic into many products. These machines inject molten plastic into a mold, where it cools and takes shape.
The injection molding machine‘s heart is the barrel. Here, plastic pellets get melted. A screw pushes the plastic into the mold, which is closed tight to keep it in place as it cools.
The mold shapes the final product. It sets the shape, size, and details of what’s being made. Injection molding machines vary in size and type, from small for prototypes to big for making lots of parts. This process is versatile and efficient in plastic making.
Key Components of an Injection Molding Machine | Function |
---|---|
Hopper | Holds the plastic pellets or granules that will be melted and injected into the mold. |
Barrel | Heats and melts the plastic material, preparing it for injection into the mold. |
Screw | Rotates and pushes the molten plastic through the barrel and into the mold cavity. |
Mold | Provides the negative space that will be filled with the molten plastic to create the final part. |
Knowing how injection molding machines work helps manufacturers make better products. They can improve their plastic injection molding to meet many industry needs.
Types of Injection Molding Machine Types
In the world of injection molding, there are two main types of machines: hydraulic and electric. Each type has its own benefits and suits different needs. This lets manufacturers pick the best machine for their projects.
Hydraulic Injection Molding Machines
Hydraulic injection molding machines use a hydraulic system to push molten plastic into the mold. They are great for making large and complex parts because of their strong clamping force. These machines are often used in the automotive and medical fields where quality is crucial.
The hydraulic injection molding process gives great control during the injection stage. This helps manufacturers make precise adjustments and avoid mistakes. This control is why hydraulic machines are chosen for high-quality parts.
Electric Injection Molding Machines
Electric injection molding machines use an electric motor instead of hydraulics. They are more energy-efficient and need less power. Electric injection molding also offers better precision and consistency.
These machines are ideal for industries needing tight tolerances and consistent quality, like electronics and consumer goods. Their energy efficiency is another reason they’re becoming more popular.
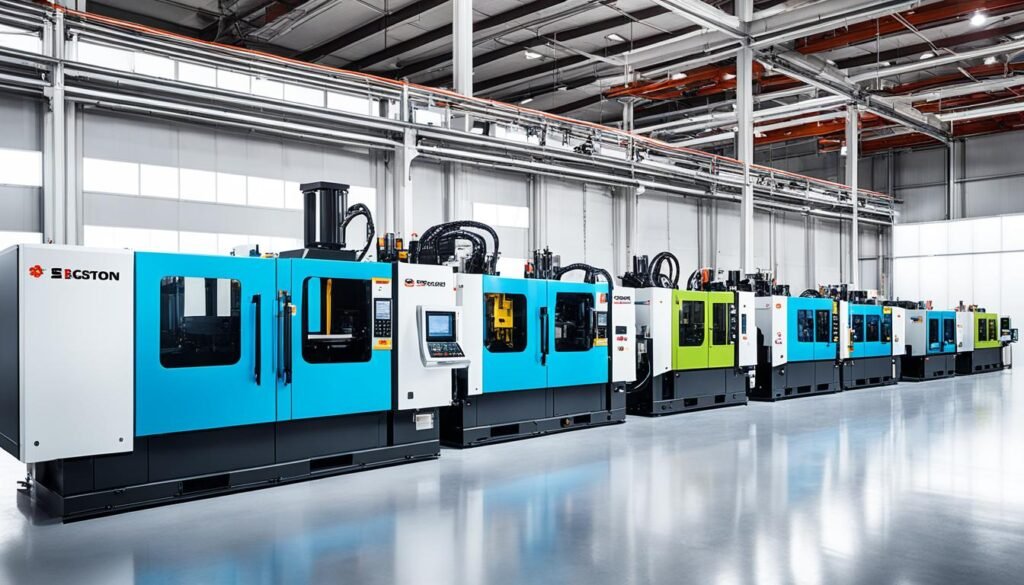
Choosing the right injection molding machine type depends on several factors. You should think about the part’s complexity, precision needed, and energy efficiency. Knowing the strengths of hydraulic and electric injection molding machines helps you make a choice that fits your manufacturing goals.
Advanced Injection Molding Techniques
The injection molding industry is always changing. Manufacturers use new techniques to make their products better, faster, and more versatile. Gas-assisted injection molding and thin-wall injection molding are two techniques that are becoming very popular.
Gas-Assisted Injection Molding
Gas-assisted injection molding uses a gas like nitrogen with the molten plastic. This method has many benefits. It uses less material, makes parts stronger, and improves their surface quality. It helps make big, hollow parts with thin walls, which are lighter and cheaper to make.
This method is great for making car parts, furniture, and other items where being light and strong matters a lot.
Thin-Wall Injection Molding
Thin-wall injection molding makes parts with walls that are very thin, often under 1 millimeter. It helps save material while keeping parts strong. This method is used a lot for packaging, electronics, and other things that need to be light and efficient.
Using this technique, companies can cut costs, make products more sustainable, and meet the demand for light, strong plastic parts.
“Embracing advanced injection molding techniques like gas-assisted and thin-wall molding allows manufacturers to stay ahead of the curve, delivering innovative products that meet the evolving needs of their customers.”
Quality Control in Injection Molding
At THY Precision, we know that injection molding quality control is key for making high-quality parts. We use top-notch injection molding machine types and strict quality checks. This ensures our customers get the best injection molding process quality and injection molding part quality.
We keep a close eye on important factors during the injection molding process. This means designing molds well, picking the right materials, and controlling things like temperature and pressure. By doing this, we can reduce mistakes and make sure the parts are accurate and strong.
We also use advanced quality control methods. For example, we have in-process monitoring systems to watch important factors in real-time. This helps us fix problems early. We also use statistical process control to make our injection molding better over time.
Quality Control Measure | Description |
---|---|
Mold Design Optimization | Carefully designing molds to minimize flow imbalances and optimize part geometry for consistent quality |
Material Selection | Selecting the appropriate materials based on part requirements and compatibility with the injection molding process |
Process Parameter Monitoring | Continuously monitoring and adjusting critical parameters such as temperature, pressure, and cycle time to maintain tight tolerances |
Dimensional Inspection | Performing comprehensive dimensional analysis to ensure parts meet the specified requirements |
Visual and Functional Testing | Conducting thorough visual inspections and functional testing to identify and address any defects or quality issues |
At THY Precision, we aim for the highest injection molding quality control for our clients. With our knowledge of injection molding machine types, advanced quality control, and a focus on getting better, we make injection molded parts that go beyond what customers expect.
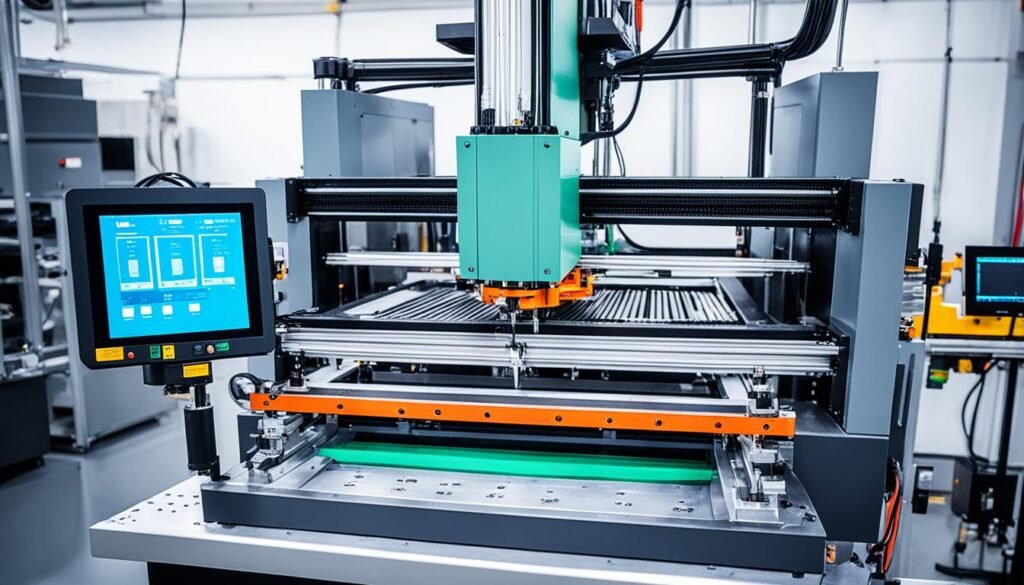
Materials and Applications
Injection molding is a versatile process that uses many injection molding materials. These include thermoplastics, thermosets, metals, and ceramics. The choice of material depends on the product’s needs, like strength, flexibility, or chemical resistance.
Common injection molding plastic materials are polypropylene (PP), polyethylene (PE), acrylonitrile butadiene styrene (ABS), and polycarbonate (PC). These plastics are great for many uses, from everyday items to car parts.
Injection molding isn’t just for plastics. Injection molding metal materials like aluminum, stainless steel, and copper alloys make strong parts for electronics, medical devices, and aerospace. Injection molding ceramic materials are used for parts that need to handle high heat and chemicals well. These are often found in industrial and technical fields.
Material Type | Characteristics | Common Applications |
---|---|---|
Thermoplastics (e.g., PP, PE, ABS, PC) | Strength, flexibility, chemical resistance, thermal stability | Consumer goods, automotive parts, electronics |
Metals (e.g., aluminum, stainless steel, copper alloys) | High strength, durability, thermal and electrical conductivity | Electronics, medical devices, aerospace components |
Ceramics | Exceptional thermal and chemical resistance | Industrial and technical applications |
THY Precision uses injection molding materials to make a wide variety of products. Our team can create everything from high-performance plastics to complex metal parts or specialized ceramics. We help our clients get the most out of injection molding technology.
Conclusion
In the manufacturing world, picking the right injection molding machine types is key to better quality and smoother production. Knowing how different injection molding machine types, like hydraulic, electric, and gas-assisted, work helps you make your production fit your products and industries.
Choosing the right materials, designing your molds well, and setting up your process right can make your injection molded parts better, more consistent, and efficient. This leads to products that work well, save money, and please your customers. THY Precision is a top name in injection molding machine types, knowing how important quality and efficiency are in making things.
Working with THY Precision means you get to use their knowledge in injection molding machine types and methods to make your production smoother, cut down on waste, and keep delivering top-notch products. Whether you’re making parts for cars, medical devices, or consumer electronics, the right injection molding machine types and methods are crucial for quality and efficiency.